plastics-sustainability-grey-is-the-new-green
May 20, 2021
Note: Conor Carlin is the editor and co-author of the forthcoming book, “Plastics & Sustainability: Grey is the New Green: Exploring the Nuances and Complexities of Modern Plastics” published by Wiley/Scrivener. This blog post has been adapted from Carlin’s opinion piece that appeared in SPE’s Plastics Engineering magazine in March, 2021.
In 2008, at the beginning of the Great Recession, I had just started a full-time MBA degree program at Babson College in Wellesley, Mass., a leafy suburb west of Boston. It was a lively time to be discussing business and finance: Lehman Brothers had collapsed, house prices were declining, and stock markets were sinking. Many conversations in the classroom and hallways about mark-to-market accounting strategies, fired colleagues in New York and London, and ethically-challenged corporate leaders signaled that this wouldn’t be a normal business school program. But then a funny thing happened: we discovered cleantech.
Let me qualify that: a small and dedicated group emerged that was fascinated with how the power of business could be harnessed to create profitable, environmentally-focused companies. Of course, solar panel and wind turbine companies were already known and established, and salty veterans of facilities management knew that “increasing net asset values” by implementing energy efficiency programs was just a fancy way to describe cost management through saving energy. Although financial markets were in turmoil and serious economic fallout was a painful reality for many families, there was still optimism about the future. We explored and debated ideas and business models associated with zero-waste initiatives, composting collaboratives, new energy financing, wastewater treatment techniques, and biobased plastics packaging. This last topic was particularly resonant for me as I was able to marry plastics (from my first career) and sustainability (my burgeoning second career). This marriage has since allowed the evolution of a deep and wide perspective on the nuances and complexities of modern plastics.
During this period, I read “The Ecology of Commerce” by Paul Hawken, a noted environmental writer and investor. In short, he explained that industrial cycles do not match natural ones, but that if we harness the innovation and entrepreneurship of human ingenuity, we might be able to rectify some of our worst environmental decisions while making better ones in the future. In additional writings, he stated that “natural capital” must be defined, developed and integrated into economic thinking. Hawken was also co-author of an eponymous book, “Natural Capitalism,” which argued that an industrial transformation is possible in the future through which “society will be able to create a vital economy that uses radically less material and energy.” For plastics, this means starting at the beginning: the design phase.
Designing for Sustainability in Plastics
Starting in the 1990s, organizations such as the American Plastics Council distributed publications providing guidelines on Designing for the Environment (DFE), Designing for Recycling (DFR), and related topics. Many of these publications’ guidelines were simply good business practice because they focused on ways of using material efficiently in a part, such as using the thinnest possible wall or gauge thickness. Other DFE/DFR guidelines concerned designing for disassembly (so that parts can be separated for recycling), designing molded-in fastening features as alternatives to separate fasteners or adhesives, and designing molded-in decorative elements as a way of avoiding external coatings and finishes, which increase plant emissions and make the part less recyclable.
Thus, new and current directions are required for more sustainable plastic parts. New designs may be needed to accommodate the properties of post-consumer recycled, bio-based, and/or biodegradable materials. Meanwhile, the consumer may need to be educated and persuaded more to recognize and accept the product changes in greener packaging, especially if there are trade-offs in functionality. The new directions for green design of plastic products need to be re-envisioned in this context for contemporary decision making in the real marketplace.
Let’s look at one sub-segment of plastics, one with which we interact every day: plastics packaging. If we look at plastics packaging in a holistic, systemic manner, we might find that it is not necessarily destined to be single use. Form and function, arguably the twin pillars of design success, must remain important. Yet designers are starting to look further afield. Incorporating Design for Environment principles at the very beginning of a product’s life cycle is pivotal to creating sustainable products and packages. Here are some elements that could be considered beyond simple utilitarianism:
- Optimize resource efficiency: How can we do more with less? If we do, will we create a Jevons Paradox?
- Use of non-fossil resources: Is a bio-based option preferable, given the form and function of the part in question? Do we understand the end-of-life considerations of the bio-based material?
- Life-cycle impact assessment: Though they are not without their challenges, LCAs offer data that can be used when measuring the environmental impact of two material options. They sometimes reveal uncomfortable findings, including higher impact scores for some biobased materials due to their reliance on fertilizers and pesticides which can lead to acidification and eutrophication.
- End-of-life: This has been lacking in design considerations until recently. If an item is easily recycled within a given infrastructure, is this the best option even if the material is fossil fuel-based? What about post-life impacts on human and ecological systems?
With each item, we need to consider tradeoffs. It seems safe to say that there is no single right answer, but this does not absolve us of the responsibility to develop tools, methodologies, and measurements to reduce the environmental impact of our consumption. And though any number of spider charts, Venn diagrams, tables, weighted averages, and matrices have been developed to measure sustainability, can we unlock a universal standard? I recently read that biodegradability is highly sensitive to local soil conditions, as might be expected. But in colder countries where soil temperatures rarely reach the requirements for biodegradability, the question arises: why should this path be chosen if the environment itself does not offer compatibility?
Minimize Material Content
Product designs must, of course, always be functional and have a good or acceptable appearance, while requiring as little plastic as possible. Apart from the benefits of a reduced environmental footprint, minimizing material content is simply good business practice that contributes to the bottom line. For common plastics, this kind of light-weighting usually depends on reducing the thickness of a product, and/or using a less dense plastic. In a rigid container, stiffening features such as ribs may allow wall thickness to be reduced. Or a container might be designed to accommodate a stiff but low-density plastic like polypropylene, rather than PET, for example. In engineering applications, thin-wall molding allows weight reduction of the entire engineered system, multiplying its benefits, especially if the system is weight sensitive, like an automobile, aircraft, or portable electronic device.
Exploit a Material’s Full Value
The full value of a material can also be exploited by reusing plastic that has already been used in a product. Incorporating high recycled content (especially post-consumer content) may require using resins with a broader range of property variations than virgin resins, due to partial degradation of the polymer that occurs during its previous processing and use. This might even require designing a more generous wall thickness, for example, to ensure adequate part strength or stiffness. The design team would need to choose whether the positive benefits of using recycled material outweigh the potential costs of greater part thickness and mass or the greater risk of part failure. They should also consult with manufacturing engineering about processing recycled-content resin to see if the resin’s melt-flow properties are acceptable and consistent enough. Here, following a concurrent engineering process that links design and manufacturing is a great help in designing for sustainability.
To encourage product recycling or reuse, designers can design component products for disassembly. Fastening points or hinges integrated into the part should allow it to be easily and cleanly separated from its assembly, especially if the component can be reused as a whole. The part’s material identification code should be easily readable on the part, whether it is a number code associated with determining its recyclability, or a clearer code explaining the part’s composition, like the ones used on plastic automotive parts.
Focus on Single-Material Designs
Using multiple materials in a design adds complexity and potential waste to a manufacturing process. It also makes a part harder (or impossible) to recycle. Thus, single-material product design, properly done, results in a potentially smaller environmental footprint. Plastics forming processes and manufacturing procedures are particularly friendly to single-material designs. These processes themselves are based on relatively simple concepts: melting or heating a raw plastic material and then molding or forming it into a product, often thousands of times each day.
Likewise, recycling processes are also made more efficient when the incoming material is homogenous. Conversely, “contaminating materials” includes a broad group of materials – any proportion of which can derail the recycling process. Broadly defined, contaminants may include adhesives, tapes, labels, coatings, paint, overmolded or co-injected polymers, molded-in inserts, pigmented plastics, blends of polymers, or filled plastics. At high enough loadings, each additive in a plastic could even be considered a contaminant, and multiple additives in plastics should generally be avoided, especially when their functions can be integrated into the polymer backbone or the design itself.
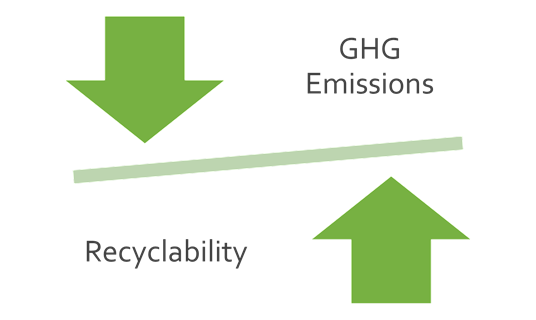
Illustrative example of tradeoffs associated with sustainability-related design decisions.(C. Carlin)
Generational Thinking
At its core, sustainability means that we—today—cannot compromise the ability of future generations to sustain themselves. The Iroquois lived by the Seventh Generation Principle: “In our every deliberation, we must consider the impact of our decisions on the next seven generations.” In a world where forecasts have proliferated with the advent of Big Data and predictive algorithms, one would be forgiven for thinking that we can surely do better when it comes to our shared planetary responsibilities. The core of plastics and sustainability, therefore, is the measurement of the impact of our material choices on the environment. If everything is equally important, then nothing is important. We must work with what we have, and develop tools to assess, measure, and manage our choices. Some choices will be hard, and they will be sub-optimal, but we cannot let the perfect be the enemy of the good.
As Paul Hawken and other environmentalists have shown, the triple bottom line of people, planet and profits is truly the best path forward. It can be done. It must be done. And we, no matter our profession, industry, vocation or location, have a critical role to play.